The most important component of electrification is the energy storage system for driving the electric motor. On the way to the high-performance end product, the life cycle of the traction battery begins with the extraction of the required raw materials.
The most important component of electrification is the energy storage system for driving the electric motor.
A battery weighing around 400 kg and with a capacity of 50 kWh primarily contains a great deal of aluminum, steel and plastics, plus around 6 kg of lithium, 10 kg of manganese, 11 kg of cobalt, 32 kg of nickel and 100 kg of graphite. By way of comparison, a smartphone battery requires about 8 g of cobalt and 8 g of lithium; for the traction battery of an electric car, therefore, about a thousand times the amount of these rare raw materials. Cobalt and lithium are the key elements for battery construction, because they are needed for the cathodes – the negative poles during charging. The anodes – the positive poles during charging – are made of graphite, a very common mineral. Every year, hundreds of thousands of tons of cobalt and lithium are mined for the production of batteries and rechargeable batteries. The steady rise in electromobility will additionally increase demand many times over in the coming years. The German Mineral Resources Agency (DERA) expects cobalt demand to increase to 225,000 t/year by 2026 (total production in 2018: 126,000 t), which compares to a global known deposit of around 7.4 million tons.
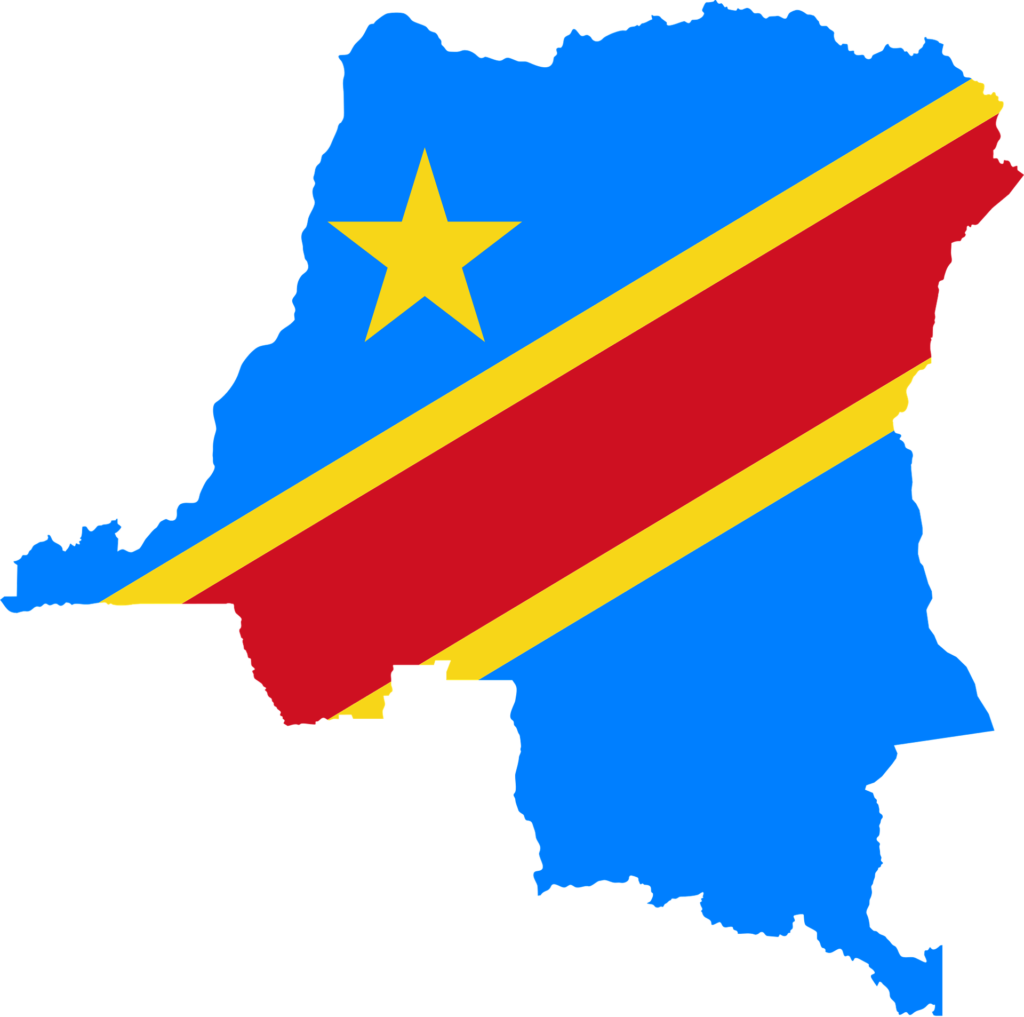
The largest proven deposit of cobalt – at 3.4 million metric tons (Mt), about half of the global reserves – is found in the Democratic Republic of Congo.
80% of the cobalt is mined industrially and 20% individually. Most mines are directly or indirectly under the power of local military leaders, who use the proceeds to finance secondary conflicts of the civil war in Congo. Thousands of children work in the mines, and people often die from fatal work accidents in tunnels and holes. Human rights violations are not taken into consideration. The world’s largest battery manufacturers are based in China, which obtains the cobalt it needs from another Chinese mining group whose subsidiary buys up smaller mines in the Congo, among other things.
German manufacturers try to avoid sourcing cobalt from Congo and buy their raw materials in Australia, for example. The fifth continent has the world’s second-largest cobalt deposit. Cobalt is also found in Canada, Cuba and Russia. In the Philippines, manganese nodules on the seabed contain the rare raw material, which is mined by deep-sea prospecting and thus poses a threat to the marine ecosystem.
Cell manufacturers are already researching methods to reduce the cobalt content in batteries. Tesla, together with its battery manufacturer Panasonic, has already reduced its cobalt content by 2.8%, whereas VW currently requires four times as much for the ID.3. But here, too, the goal is to reduce the cobalt content to below 5% in the medium term. In parallel, research is also being conducted into the development of cobalt-free batteries. Nickel would then be increasingly used instead of cobalt.
Unlike cobalt, lithium, the second key element for battery production, is not particularly rare in geological terms; the challenge lies in the different mining methods of the various deposits. In Chile, for example, the country with the largest lithium deposit in the world, it is extracted from highly pumped groundwater. The companies involved are considered corrupt, to the detriment of the indigenous population. The consequences of lithium mining are parched regions and often untreated wastewater with as yet unexplored ecological damage.
In the context of the new electric vehicles, which are frequently associated with sustainability, the focus is rarely on the ecologically questionable extraction of raw materials. It is therefore all the more gratifying that both the vehicle and battery industries are taking a critical look at the issue. In their efforts to bring ever more powerful batteries to market, they are also evaluating the extraction and origin of raw materials and trying to optimize them in terms of sustainability.